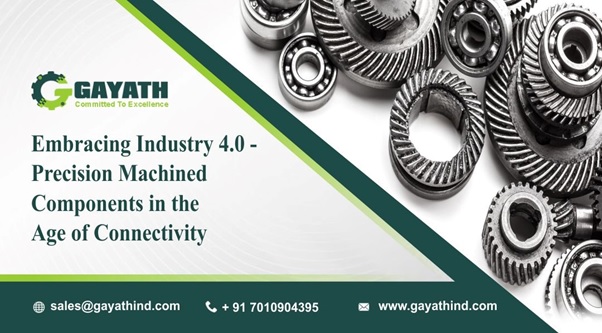
Precision Machined Components in the Age of Connectivity
Embracing Industry 4.0: Precision Machined Components in the Age of Connectivity.
In the dynamic landscape of modern manufacturing, Industry 4.0 has emerged as a transformative force, reshaping industries and processes. At the heart of this revolution lies the integration of advanced technologies into manufacturing operations, leading to improved efficiency, enhanced quality, and unprecedented levels of precision. One area that stands to gain immensely from this revolution is the production of precision machined components.
The Fusion of Precision and Connectivity
Precision machined components have long been the backbone of industries ranging from aerospace to automotive, medical devices to electronics. The demand for these components, which are vital for ensuring seamless functionality and reliability, has only grown with time. What Industry 4.0 brings to the table is a seamless fusion of precision craftsmanship with the power of connectivity and data analytics.
Key Enablers of Industry 4.0 for Precision Machining
1. Smart Manufacturing: Industry 4.0 introduces intelligent manufacturing systems that are capable of real-time monitoring and adjustment. With sensors embedded in machinery, manufacturers can capture crucial data such as temperature, vibration, and tool wear. This data-driven approach enables predictive maintenance and minimizes downtime.
2. Data Analytics: The mountains of data generated during precision machining can now be harnessed for strategic decision-making. Advanced analytics can identify trends, optimize processes, and enhance overall efficiency. Real-time data insights enable manufacturers to make informed choices that lead to reduced waste, improved resource allocation, and higher productivity.
3. Automation and Robotics: Industry 4.0 brings forth a new era of automation, where robots and machines work seamlessly together. In precision machining, this means increased accuracy, reduced human error, and the ability to tackle intricate designs and complex geometries with ease.
4. IoT Integration: The Internet of Things (IoT) is the backbone of Industry 4.0, connecting machines, tools, and systems in a comprehensive network. For precision machining, this translates to real-time monitoring of every aspect of the process, enabling operators to intervene and optimize operations as needed.
5. Augmented Reality (AR) and Virtual Reality (VR): These technologies enhance the training and guidance of operators. Complex machining operations can be simulated in a virtual environment, allowing operators to refine their skills and ensure precision even before actual production begins.
The Future of Precision Machined Components
As we embrace Industry 4.0, the landscape of precision machining is set to evolve dramatically. Components manufactured with the integration of these technologies exhibit unparalleled precision, consistency, and reliability. Manufacturers can expect reduced lead times, minimized waste, and an increase in complex designs that were once deemed unattainable.
In conclusion, the convergence of Industry 4.0 and precision machined components is a testament to the boundless possibilities that lie ahead.